深度解析直线导轨:从原理到应用的全面指南
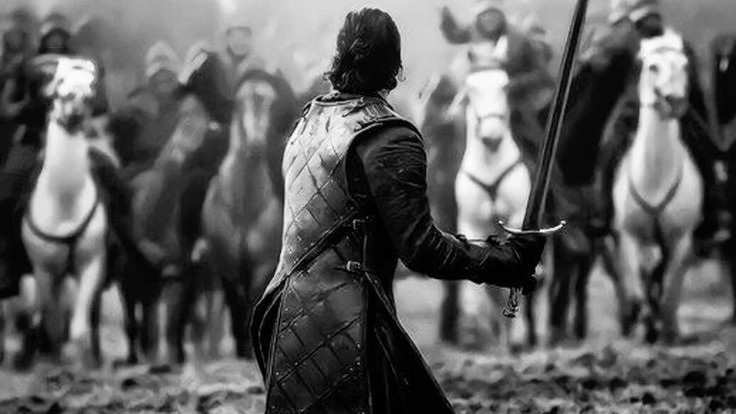
引言
在现代工业自动化和精密机械领域,直线导轨(Linear Guide Rail) 作为线性运动系统的核心组件,其重要性不言而喻。从 数控机床 的高速切削,到 工业机器人 的精准定位,再到 3D打印机 的细腻成型,直线导轨以其低摩擦、高刚性、高精度和长寿命的特性,为各类设备提供了可靠的运动支持。它不仅是机械设计的“骨骼”,更是 工业4.0 时代实现高效、智能生产的关键技术之一。
本文将从直线导轨的基本原理出发,深入剖析其结构、类型、选型要点及应用场景,并探讨其维护方法和未来发展趋势。通过详实的技术分析和实际案例,为工程师、设计师和行业从业者提供全面而深入的认识。
一、直线导轨的基本概念与工作原理
1.1 什么是直线导轨?
直线导轨 是一种机械传动元件,用于在预定直线路径上引导和支撑负载的运动。它由 导轨(Rail) 和 滑块(Carriage 或 Block) 组成,通过 滚动元件(如滚珠或滚柱)实现低摩擦的线性滑动。与传统的 滑动轴承 相比,直线导轨通过滚动摩擦替代滑动摩擦,大幅降低了摩擦系数(通常从 0.1-0.3 降至 0.001-0.005),从而提升了运动效率和精度。
1.2 工作原理
直线导轨的核心在于滚动摩擦的运用。滑块内部嵌有循环滚动的 滚珠 或 滚柱,这些滚动元件在导轨的精密滚道上运动,减少了接触面间的直接摩擦。例如,一个典型的 滚珠直线导轨 可能采用四排滚珠设计,滚珠沿 45° 接触角分布,形成“X”或“O”型排列。这种结构不仅均匀分散负载,还增强了抗扭转和抗侧向偏移的能力。
与滑动轴承相比,滚动摩擦的优势在于:
-
低能量损耗:摩擦系数低,减少驱动电机功率需求。
-
高运动平稳性:滚动元件避免了滑动时的“爬行”现象。
-
高精度保持:减少磨损,确保长期运行的定位精度。
1.3 结构组成
直线导轨的性能依赖于其精密的结构设计,主要部件包括:
-
导轨:采用高强度钢材(如中碳钢或不锈钢),表面经淬火硬化(硬度达 HRC58-62)和超精密研磨,确保直线度(偏差通常小于 0.01mm/m)和耐磨性。
-
滑块:内部装有滚动元件循环通道,通常配备润滑孔或油脂槽以维持低摩擦运行。
-
滚动元件:滚珠(直径 3-10mm)或滚柱(长度 5-20mm),材质多为轴承钢(GCr15),根据负载和速度需求选择。
-
端盖与密封件:防止灰尘、切屑进入滚道,保持润滑剂(如锂基脂)不外泄,延长使用寿命。
-
保持器:固定滚动元件位置,防止其脱落或偏移。
这种模块化设计使得直线导轨能够在高负载、高速或恶劣环境(如高温、多尘)下保持稳定运行。
二、直线导轨的主要类型
2.1 滚珠导轨(Ball Guide Rail)
技术特点:采用滚珠作为滚动元件,滚道设计多为哥特式弧形(两点接触)或圆弧形(四点接触)。滚珠的点接触特性使其摩擦系数极低(约 0.001-0.003)。
优势:
-
高精度:定位重复精度可达 ±0.003mm,适合精密加工。
-
高速度:运行速度可达 3-5m/s,部分高端型号(如 THK 的 SSR 系列)可达 10m/s。
-
低噪音:滚珠滚动平稳,噪音低于 50 分贝。
局限:点接触导致承载能力相对较低,对灰尘和异物敏感,需配备高性能密封件。
典型应用:数控机床主轴、半导体晶圆搬运设备。
2.2 滚柱导轨(Roller Guide Rail)
技术特点:使用滚柱替代滚珠,滚柱的线接触设计(接触面积是滚珠的 10 倍以上)显著提升刚性和承载能力。
优势:
-
高刚性:额定动态负载可达滚珠导轨的 2-3 倍。
-
高抗扭性:适合承受多方向力矩的应用。
局限:摩擦系数略高(约 0.005-0.01),运行速度上限较低(一般不超过 3m/s),噪音稍大。
典型应用:重型机械(如龙门铣床)、工业机器人关节。
2.2 其他特殊类型
-
微型导轨:尺寸小(宽度 5-15mm),滚珠直径仅 1-3mm,适用于医疗仪器(如 CT 机滑台)、小型 3D 打印机。
-
自润滑导轨:内置润滑模块(如油毡或聚合物储油槽),可实现数万公里免维护运行,适合无人值守设备(如风电设备)。
-
交叉滚子导轨:滚子交叉排列,兼具高刚性和紧凑性,常用于光学仪器和高精度平台。
三、直线导轨的选型要点
3.1 负载能力
负载分为静态负载(设备静止时的最大承受力)和动态负载(运行时的承受力)。制造商提供额定负载数据:
-
C0(静态额定负载):滑块在静止状态下可承受的最大力。
-
C50(动态额定负载):在 50 公里行程下,90% 可靠性时的负载值。
案例:一台数控机床工作台需承载 500kg 动态负载,运行速度 2m/s,选型时需选择 \( C50 \geq 5000 \, \text{N} \)(约 \( 500 \, \text{kg} \times 9.8 \, \text{m/s}^2 \))的导轨。
3.2 精度等级
精度等级反映导轨的制造公差和运行稳定性,常见标准(如 DIN 或 JIS)包括:
-
N级(普通级):平行度偏差约 0.02mm/m,适用于一般自动化。
-
H级(高级):偏差约 0.01mm/m,适合中等精度设备。
-
P级(精密级)及以上:偏差小于 0.005mm/m,用于半导体制造等超高精度场景。
选型建议:根据设备定位精度需求选择,避免过度追求高精度增加成本。
3.3 速度与加速度
滚珠导轨支持 3-10m/s 的速度,滚柱导轨通常低于 3m/s。高速应用需考虑滚珠循环的热效应。高加速度(\( > 5 \, \text{m/s}^2 \))会增加滚动元件的惯性载荷,需选择预加载较高的型号(如中预载 ZH 或重预载 ZG)。
3.4 环境适应性
环境条件对导轨选型至关重要:
-
多尘环境:选用带双唇密封件或刮板的设计(如 THK 的 SRS 系列)。
-
腐蚀环境:选择不锈钢导轨或镀铬涂层,耐腐蚀性提升 50% 以上。
-
高温环境:采用耐高温润滑脂(如氟化脂)和特殊材质(如耐热钢)。
3.5 安装与对齐
安装面平整度误差应小于 0.02mm/500mm,双轨平行度偏差超过 0.01mm/m 可能引发滑块卡滞或滚珠脱落。
案例:某机器人制造商因安装面未达标,导致导轨寿命从预期 10 年降至 3 年。
四、直线导轨的应用场景
4.1 工业自动化
应用:传送带、机械臂、自动装配线。
案例:汽车制造中,焊接机器人采用滚柱导轨支持 10kg 焊枪,运行速度 1.5m/s,确保 ±0.1mm 的焊接精度。
4.2 数控机床
应用:主轴移动、工作台定位。
案例:一台五轴加工中心使用滚珠导轨,速度 5m/s,重复定位精度达 0.002mm,满足航空零件加工需求。
4.3 3D打印与机器人
应用:3D 打印机打印头、机器人多轴关节。
案例:某工业级 3D 打印机采用微型导轨,行程 300mm,精度 ±0.01mm,实现复杂模型的高质量打印。
4.4 物流与包装
应用:分拣系统传送带、升降机构。
案例:某电商物流中心使用滚珠导轨驱动分拣线,每小时处理 5000 件包裹,运行平稳性提升 20%。
五、维护与寿命优化
5.1 寿命计算
直线导轨的寿命以滚动距离(公里)衡量,计算公式为:
$$ L = \left(\frac{C}{P}\right)^3 \times 50 $$
其中:
-
\(L\):寿命(公里)
-
\(C\):额定动态负载(牛顿,N)
-
\(P\):实际负载(牛顿,N)
案例分析:假设一台设备的导轨额定动态负载 \( C = 10000 \, \text{N} \),实际负载 \( P = 2000 \, \text{N} \),则寿命为:
$$ L = \left(\frac{10000}{2000}\right)^3 \times 50 = 5^3 \times 50 = 125 \times 50 = 6250 \, \text{公里} $$
这意味着在理想条件下,该导轨可运行 6250 公里而保持 90% 的可靠性。
5.2 维护要点
-
润滑:每 3000-5000 公里补充锂基润滑脂,减少磨损 50% 以上。
-
清洁:用无纺布擦拭滚道,每月检查密封件状态。
-
检查:用测力计检测滑块阻力,异常时调整对齐或更换润滑剂。
六、未来发展趋势
6.1 智能化
技术:集成传感器监测负载、温度和磨损,实时反馈至控制系统。
前景:预测性维护可将停机时间减少 30%。
6.2 轻量化
技术:采用铝合金导轨或碳纤维复合材料,重量降低 20%-40%。
前景:适用于航空航天和移动机器人。
6.3 高性能化
技术:优化滚道设计和润滑系统,速度提升至 15m/s,负载能力提高 50%。
前景:满足超高速加工和重载应用需求。
结语
直线导轨 不仅是现代机械的“骨骼”,更是推动工业智能化和精密化的基石。从滚珠导轨的高速精密,到滚柱导轨的重载刚性,再到微型导轨的灵活应用,它在各领域的表现令人瞩目。对于工程师和管理者而言,理解其原理、选型和维护是优化设备性能的关键。展望未来,随着智能制造的深入,直线导轨将在更高速度、更强负载和更广场景中发挥无可替代的作用。
✨ END ✨
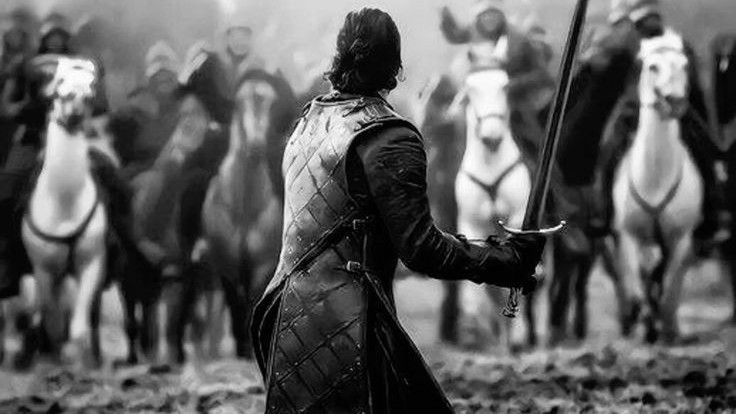